Benefits of UltraGenizer High Pressure Homogenizers
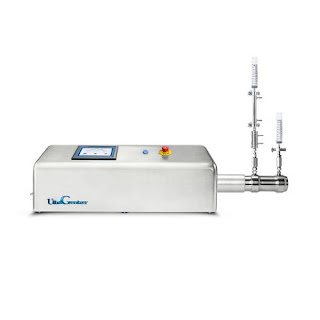
Benefits of UltraGenizer High Pressure Homogenizers UltraGenizer Microfludic High Pressure Homogenizers represent a notable advancement when it comes to achieving precise and efficient homogenization of various materials. Designed to meet the demands of cutting-edge research and industrial applications, these homogenizers offer a host of benefits that set them apart. Let's delve into the advantages that make UltraGenizer stand out: UltraGenizer Microfluidic High Pressure Homogenizer 1. Unmatched Pressure Control: With a maximum design pressure of 60,000 psi, UltraGenizer allows users to fine-tune the pressure settings through an intuitive touchscreen interface , ensuring easy and user-friendly operation. 2. High-Performance Flow Rate : The homogenization flow rate can reach a maximum of 100 ml/min, providing exceptional flexibility and adaptability for different materials and viscosities. 3. Customizable Sample Intake : UltraGenizer enables users to set their desired sample